Any Master of Fine Arts student knows that a vital part of an art class, albeit dreaded, is the ‘crit.’ Partly a rite of passage in which we sometimes endured the ‘ugly stick,’ the classroom critique served to prepare us to analyze and evaluate our artwork upon graduation.
As art students, we haphazardly learned the Principles of Design which led us to investigate various frameworks for artistic reflection and allowed us to construct our foundation for self-critique eventually. We asked ourselves the following questions when designing something as seemingly simple as a mug. Does the piece have the right visual weight? Is it visually balanced? Does the handle leave a pleasing ‘negative space’ silhouette? Does the handle flow out of one line and into another? Are the beginnings and endings of the pots intentional? Are changes in planes emphasized? Most importantly and more elusive, does the pot reflect my artistic influences and personal philosophies? That seems like a tall enough order for a mug, but more questions must be asked. As potters, we must go beyond design basics and personal choices to ponder functional considerations.
How will this mug feel in someone’s hands? Is the texture too sharp? Is the physical weight right? Is the handle close enough to keep from putting a strain on the wrist when filled with liquid? Will the mug tip over when filled up? Is the rim too flared so that coffee will easily splash out? Is the handle attachment secure? Is the handle placed in a way that enhances the form while still comfortable? Will the rim feel natural when one puts their lips on it? Will the liquid flow over the rim when drinking? Should it have a foot-ring? Is the base too wide or too narrow, or just right?
Even though it has been many years since Kent and I were MFA students, we embrace lifelong learning and continue this evaluation process. Sometimes, we make rapid artistic decisions intuitively, while others take more deliberation and time. Kent and I spent several years in school studying historical forms, solving visual design problems, sketching pots, and making thousands of pieces we used and analyzed. I don’t mean to overstate the work involved. It was challenging, but we also experienced much joy from this process and still do! Like then, Kent and I often act as sounding boards for each other. Our dining room is a veritable “Test Kitchen” for form and function. And we listen to our customers.
Recently, a few customers mentioned that espresso mugs should be smaller than the mugs we had made. Most of our espresso mugs at home have become water cups for kiddos because they are difficult to knock over, have a lower center of gravity, and have a smaller handle perfect for little fingers. We don’t drink that much espresso except for Kent’s occasional Caffe Americano. Hearing from customers that the espresso mugs needed to be a little smaller was an excellent opportunity for a ‘redesign.’ Kent has spent several weeks making more petite espresso mugs, and we wanted to share some photos. If you like what you see, check them out on the mug rack at Blue Sage Pottery.
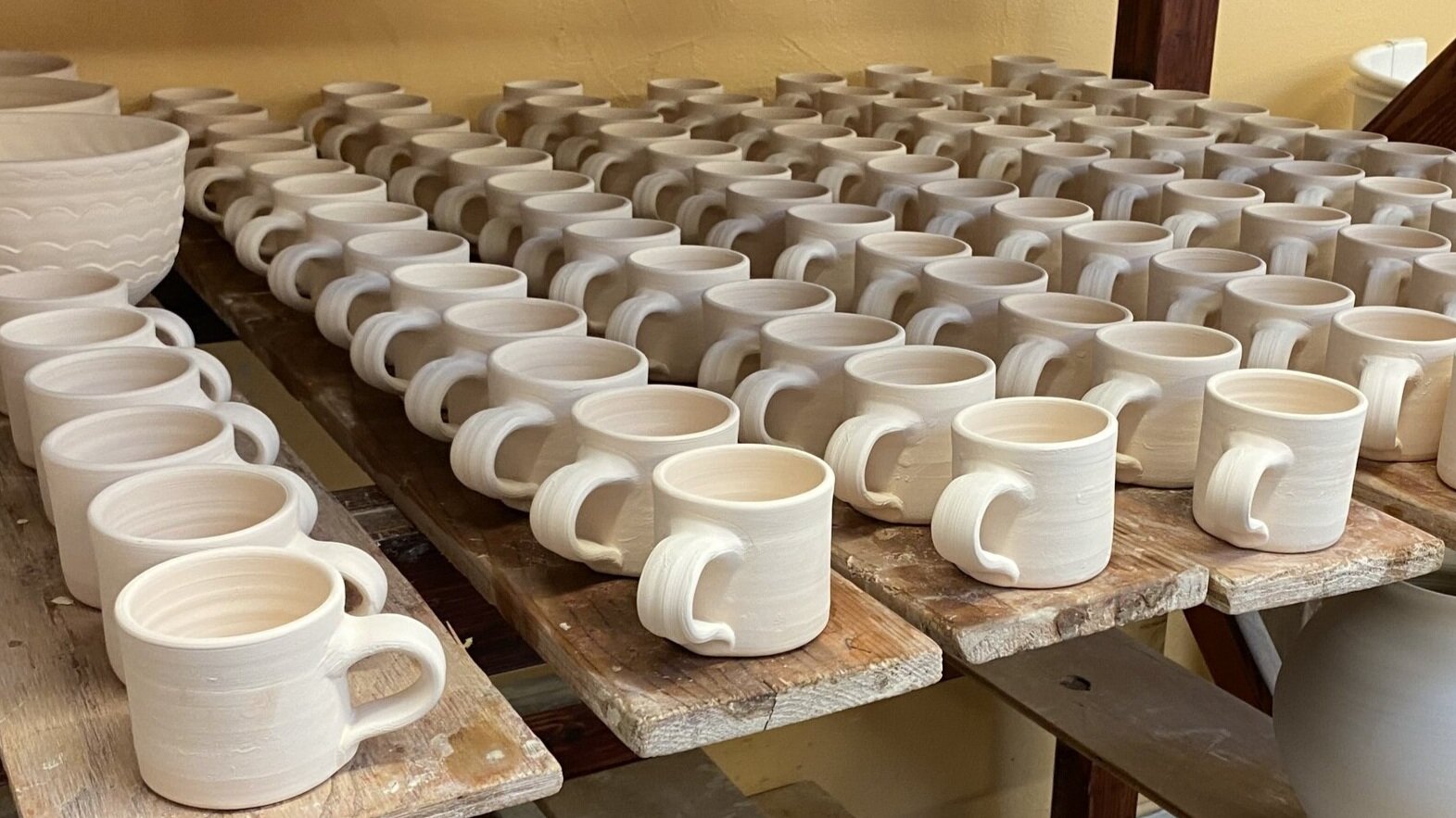
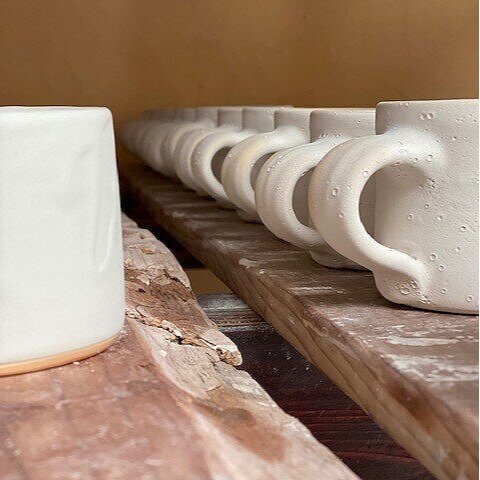
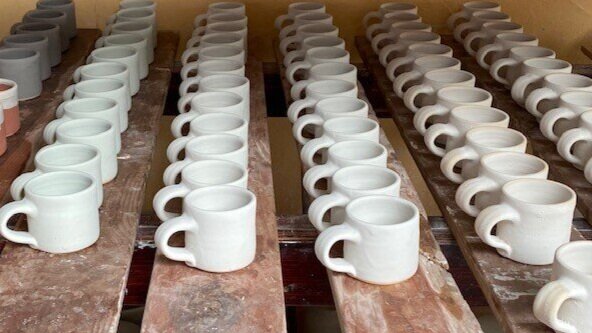
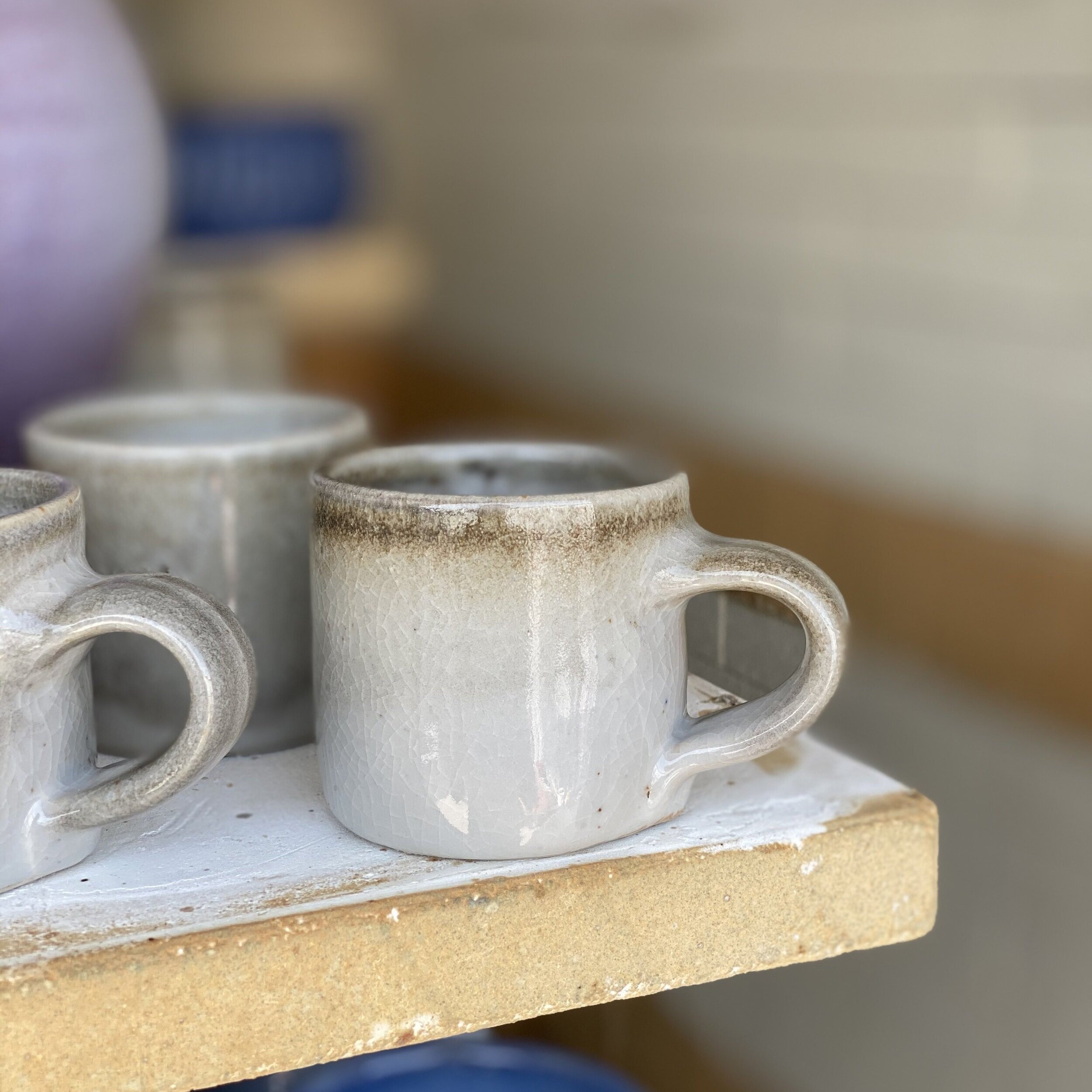
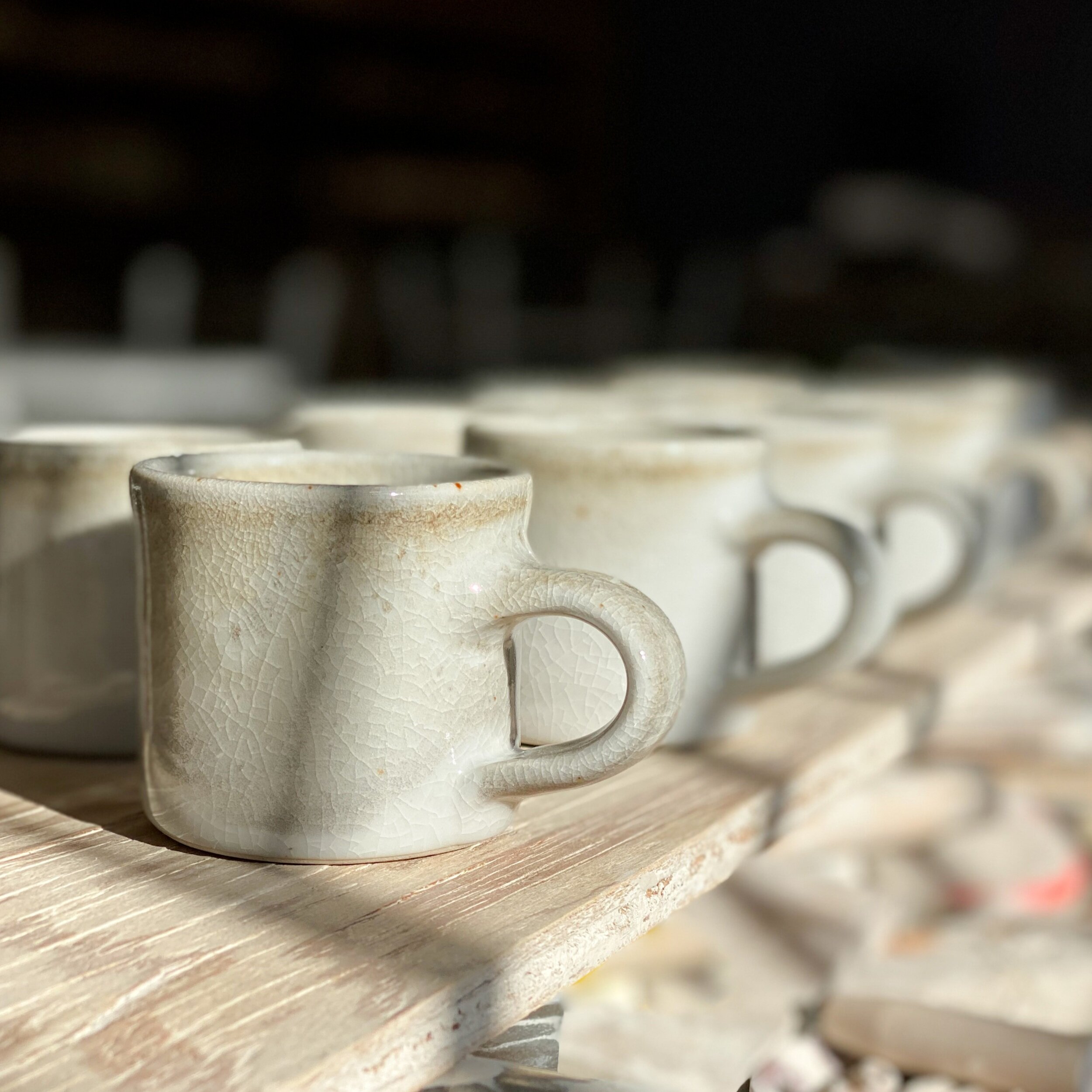
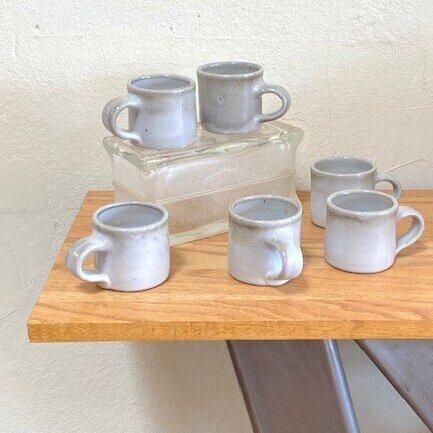